A dry bilge for $50

Water in the bilge, even small quantities, is a recipe for bad smells and generally unpleasant results. Every boat I’ve owned accumulated water somewhere that a traditional bilge pump couldn’t entirely remove. I’ve long been aware of commercial kits designed to completely dry bilges, but the problem never got high enough on my list to spend the money. Recently I came across an article on how to build your own dry bilge system and decided to give it a try. The results are impressive and the cost low.
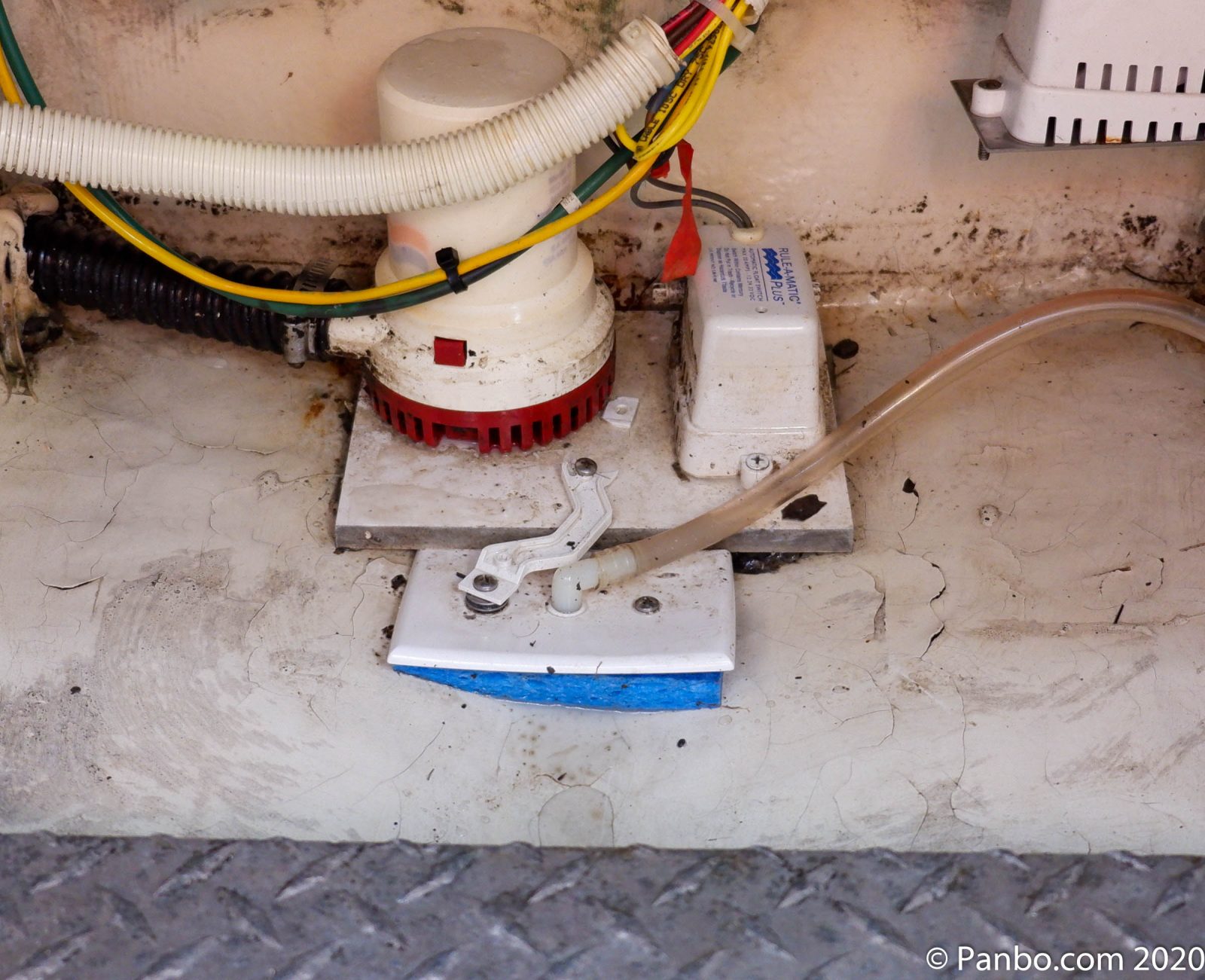
The system consists of one or more homemade water pickups, a small (1.3 gallon per minute) diaphragm pump, and some plastic tubing. The author of the article used three such pickups and a small manifold before the pump. Have Another Day only has one area that typically has water and the rest drain back to it, so I only used one pickup, and thus didn’t have to construct a manifold or deal with differing tubing diameters as described in the article. But early on in my use, the pump became clogged with crud from the bilge so I added a small inline screen filter.
The pickup itself is an electrical plate cover, a sponge, and a 90-degree hose barb to threaded adapter. I drilled holes in the side of the threads on the barb adapter to allow it to draw water through the sponge. I also hollowed the sponge out for the barb adapter and then ran two stainless screws through the plate and the sponge to hold it together.
I used 3/8-inch inside diameter tubing and a 3/8-inch to 3/8-inch elbow of the pickup. The electrical plate cover I bought came with the little arm you see pictured that provided a way to anchor the micro-pickup to the main bilge pump’s plate. That arm and a few washers on the screw through the plate helped me force the sponge down to the bottom of the bilge.
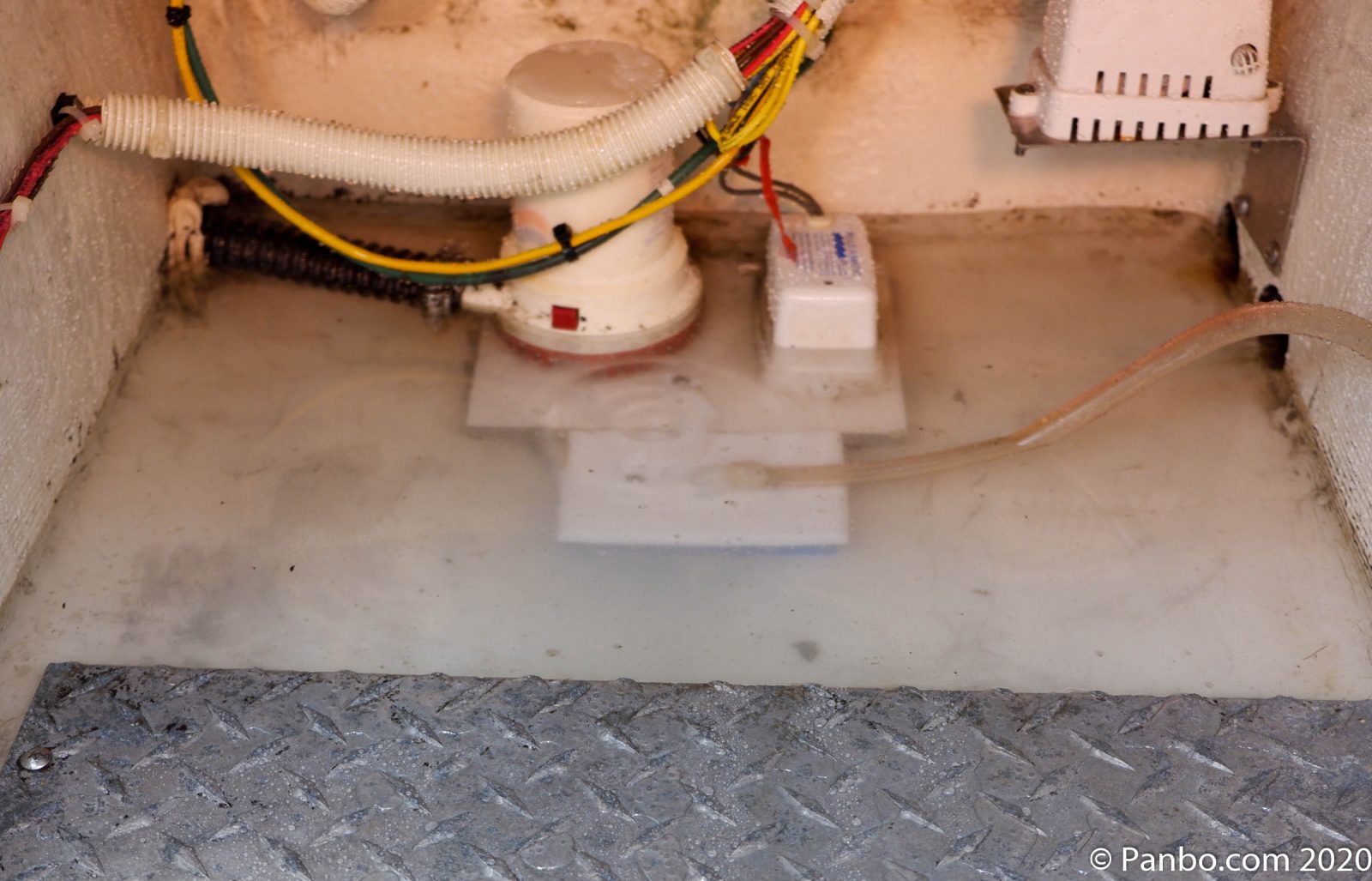
Have Another Day sits stern low so any water in any bilge area eventually makes it’s way back to the aft bilge. The float switch and bilge pump are mounted on a board raising them about an inch and a half over the lowest point of the bilge. The couple of inches the float switch needs to turn on combined with the raised mounting position mean that quite a bit of water can collect in the aft bilge and won’t be evacuated by the main pump. The dry bilge pump is able to get the bilge down to just a few drops of water, though it does take about 10 minutes to empty the bilge when it’s at the level in the picture above.

The author of the article uses a small timer to control his dry bilge system and that seems to work well for him. Never content with a simple solution, I got a little more involved in controlling my dry bilge system. Now the power is managed by a Maretron MPower CLMD12 digital switch with current metering capabilities. Knowing that pumps draw more power when they’re moving water than when they’re pumping air I figure it was likely I could use the CLMD12’s current metering to determine if water was still moving. It turns out the pump draws about 1.5 amps with water flowing and 0.7 amps when it’s just moving air.
I use SignalK Server and the Node-Red plugin to turn on the pump at 8pm every night and then watch how much current the pump is drawing. First, the node I defined lets the pump run for one minute. Then, if the pump has run for more than one minute and is drawing less than 0.8 amps, it’s turned off. Thus far this setup has worked perfectly to turn run the pump long enough to make sure the bilge is dry after each run.
I believe my total investment in this project is right around $50. I am leveraging other components already on the boat to control the system but if I didn’t have them I could easily use a timer or even just a toggle switch. Regardless of how it’s controlled, I can’t believe how easy and productive a project this was. I’ll reap the benefits of the small investment in time and money in the form of a drier, less stinky bilge for years to come.
Ben,
Where did you route the discharge? It seems to me that is always a key issue for these systems. I hate to install more through hulls and combining discharges is also frowned upon.
I would like to solve this issue on Crackerjack since it lies bow low so you have to lay over the engines to mop each hull dry.
All the best
I was able to route into a deck drain elbow. It discharges well above the waterline already had a couple of drains meeting so I didn’t feel this was an unreasonable risk to take. I suppose it’s possible that if the discharge of the drain were sufficiently backed up it might drain towards the bilge but I’m not sure the pump would allow the water through and even if it did the main bilge pump would be able to evacuate the water. Plus if those drains backed up they’d overflow into the bilge as well so it’s effectively the same risk.
-Ben S.
I would pump it into a cockpit near a cockpit drain myself, but that might annoy some people (stains etc). I have run similar ones into outboard motor wells before (thou those are less and less common). On some larger power yachts I have worked on I have seen the Arid bilge tied into sink drains well above the water line several times. A siphoin break above the sink would prevent most issues in that setup.
Since MIBS, I have been slowly working on this project too after seeing a COTS system that is sold by the pump manufacturer on Amazon for a very reasonable, though not $50 (!), price. Thanks for the thoughts on drain spots. That has been slowing me down. I am thinking about building another for my shower sump , which always has nasty water in it. Where did you find the filter? I am going with a timer (per article) but you now have me wondering about Rhasperry Pi for intelligence. I am never going to complete my boat to-do list.
Same principle as the Rule 25SA 500GPH bilge pump that I have been using in my PWC’s for years. For me they have worked well, but they are susceptible to getting “crudded up”, which flummoxes the current-sensing. I’ll be interested to see how the long term reliability works out for you.
Well done!
Looks like a nifty little pump…
https://www.amazon.com/Rule-25SA-Electronic-Sensing-Bilge/dp/B0719D2HSX
… but I don’t see how it could attain the same level of “dryness” as what Ben S put together.
I was just commenting on the technology. You’re 100% right…. it will never get a bilge dry.
You probably noticed the strainer style filter on the pump inlet; without that filter the pump tends to get jammed with debris. With that filter in place it’s been running for over a month without any issues.
As for the current sensing side of the house I’m only about six weeks into running it but I’m very happy with how it’s working. Most nights it runs for exactly one minute. If I’ve done something in the engine room to spill a little water it might run slightly longer. I think I’m going to add a step to send me a summary email after the pumping session is over. That way I can know how long it ran and the current consumption over that time period.
-Ben S.
Ben, when I follow the link to the Maretron digital switch, I’m taken to a $500 switch. Is there another option?
Chuck,
The Maretron CLMD12 I used is a very capable, 12 channel, fully functional digital switching system. It’s certainly overkill if its only job is to control the dry bilge system. You could use less expensive digital switches like a C-Zone Contact 6-plus or a Yacht Devices YDCC but neither of those will measure current. So, you could add a Yacht Devices YDRI which does measure current. But, by the time you’ve done that you’re getting close to the cost of the Maretron switch. It would likely be most cost effective to go with a simple timer like what’s suggested in the original how-to that I link to in the article.
-Ben S.
an easier solution is to use an Arduino, which measure the current. Then you can also use the Arduino to adjust the ‘check’ interval time between going on. Currently the ‘wait time between ‘check pumps’ is between 15 sec to 2 days.
The 25SA is just goblins up energy by turning on every 2 1/2 minute
This article got me thinking… as I have a perpetually wet bilge(s) in the Christina B, primarily due to condensation from my chilled water air handlers.
As I mentioned in a comment above, the control circuitry and monitoring that Ben put together reminded me of what is built into the Rule 25SA. So I decided to do an experiment.
I bought a new 25SA and did some current monitoring so I could roughly figure out where they have the current threshold settings for running the pump. Then I tore the little sucker apart to expose the motor and control board.
Then I bought the same diaphragm pump that Ben and the other author used. I did some quick instrumentation.. and noted that my numbers agreed with Ben’s.
Then I just hooked the diaphragm pump in direct parallel with the motor for the Rule pump. Based on my calculations, depending on the margins and how Rule did their code, this *might* work without further modification to the board.
To my joy (OK… perhaps surprise) it worked right out of the box. The pump turns on, and if there is water to be pumped it will run until the pump runs dry (there is enough delay in the system to allow the pump to prime with a 3′ inlet hose). If the pump is already dry, the pump will shut off after about 10 seconds. Then the auto-timer will cycle every 2.5 minutes… checking for water presence.
So this basically ends up performing like Ben’s rig (which I really like), but you don’t have to have the peripheral equipment that he already had installed on his boat. You don’t need to do any current sensing or write any code.
I’ll continue to mess with it to make sure that it performs as expected under variable conditions. If need be I can remove the Rule motor completely and/or modify the current-sensing resistor that is installed on the Rule board. My knee-jerk is to remove the Rule motor, but I’m trying to keep the modification as simple as possible.
If it all continues to work well here on the bench, I’ll 3D print up a nice enclosure for the motor/board and install it on one of my bilges the next time I run down to the boat.
If my calculations are correct…. I could actually leave the entire centrifugal pump portion of the rule in place and actually use both pumps (Rule and diaphragm). The Rule 500GPH could do the “heavy lifting” if the bilge has a lot of water in it (it will pump down to about 1/2″…. way below what my big pump will do) and then let the diaphragm pump do the finish work. All off of the same circuit.
I’d still leave the Rule 3700 and float switch in place to do the “really heavy lifting”.
Scott, I’d love to hear more about your findings from your experiment and testing.
Also, if you wire the diaphragm pump in parallel with the motor in the rule pump, is the combination of the two motors running at the same time possibly too much load for the circuitry?
Chuck,
Sorry for the delay in my response.
Guess I’ve been running this setup for well over a year now, and I’m quite happy with the results. The 25SA has had no problems at all running the diaphragm pump in parallel, and after a little tuning, the “water sensing” has basically worked without a hitch. I have it all pretty well instrumented with my Maretron and Yacht Devices hardware, so I can see the ~1s current blips about every 2.5 minutes. Typically, that will be it… but when water builds up (enough to saturate the sponge) the pump will kick in and cycle until the current draw drops below the threshold (about 3A) and then turn off. That will usually get all of the water, but on occasion two or three subsequent cycles are required. Doesn’t bother me… the bilge is usually dried out within ten minutes.
This has been one of the few things on the boat that I’ve implemented that has truly been “set it and forget it”.
Scott,
Wondering if this is still working and if you have any pictures of the setup? I’d like to try something similar but would like to see how you accomplished the wiring between the 25SA pump and the diaphragm pump. Do you cut off the red top of the rule to expose the wiring?
Thanks
wow – thanks for the information
I installed a total of nine pickups using two pumps and two timers. They each run twice a day for five minutes and the bilge has dust in it since it’s so dry.
I took the two 3/8″ discharge hoses (one from each pump) and pressure fit it into the 1.5″ hose from the deck drains. Since there isn’t any pressure in these drains, it works just fine with the pressure fit.
Here’s my issue: there are two drains in the cockpit that use these drain hoses. When the pumps turn on, there’s a considerable amount of noise that come out of the cockpit drains, especially if the sponges are dry and the pump isn’t moving water. If it’s moving water, it’s quieter. Any suggestions on how to quiet this? It is pretty annoying and can be heard a couple of boats away when in a marina. We’re in Marathon now and I’ve turned the timers off so not to disturb anyone.
Other than the noise, the system works great. Since I have a lot of Maretron equipment on Leeway, I may eventually monitoring like Ben’s system.
Thanks,
Kevin
Nice setup!
If you send the pumps less voltage do they run quieter?
Although you can try experimenting a little, I haven’t had any luck with this approach. My experience is that dropping the voltage just changes the pitch of the pump and reduces efficiency.
-Ben S.
Ben, I’m reproducing this dry bilge system. Why the sponge. Why not just have the hose terminate 1/32 of an inch above the floor of the bilge? Does the pickup actually suck water out of the sponge or does it just get air?
Harry,
The sponge design wasn’t mine, I copied what others have suggested. But, I think that I’ve observed that the sponge soaks up the water in the area and the pickup then sucks the water out of the sponge. I’m sure the system would be effective without the sponge but I can’t say it would be as effective.
-Ben S.
is there a water sensor commercially available with a relay that would be able to turn on the pump when water is in the bilge – rather than a timer that turns on the pump periodically whether there is water present or not?
Here’s one that appears to triggered by the conductivity of the water itself. I’m not so sure how well it will work in a tiny amount of water.
https://waterwitchinc.com/wp-content/uploads/2015/11/Model-217-Series.pdf
I built the project including a through-hull to discharge the water, used the pump and filter recommended and it’s great.
So I’m moving from proof of concept which simply used a push button switch, to a timer specifically the very popular grt8-s2. I brought the switch , it is energized, it’s starting and stopping the pump depending on where I turn the knobs but for the life of me, I don’t understand how I would make it turn on for 2 minutes every 6 hours or something like that. There are two knobs, time and percentage. Does anybody have experience with any of those grt8s?
Thanks for this great info. I’m looking forward to tackling this project soon.
Is there a reason why you wouldn’t use an electronic switch like the Whale BE9006 in place of the timer?
https://www.hodgesmarine.com/whabe9006-whale-electric-field-bilge-switch-with-time-dela.html?gclid=CjwKCAiAiKuOBhBQEiwAId_sK-7E4o_ylCg2HvMdTwTAZeNJM5GxahoMUMAGk5lzklkFiqRuu_JKqBoCT64QAvD_BwE
it does not switch on until 2 inches of water is reached
ah, thanks. That’s a good reason!
Hi! I was wondering if anyone has opinions on building the manifold.
I’m wondering if it’s best to have the manifold closest to the pump, or closer to the pickups. Also, is it advantageous to make all of the 1/8” pickup tubes the same length?
Man, I would do this system in a heartbeat, if someone could point me to a 12v timer that would turn it on once or twice a day for a minute or two. Any leads on this? Thanks!
Here’s the timer I used in building my system:
https://smile.amazon.com/gp/product/B012FSL2GK/ref=ppx_yo_dt_b_search_asin_title?ie=UTF8&psc=1
I turn it on twice a day for two minutes. Bilge dry as a bone.
Here’s a link to photos of my system and a list of parts: https://1drv.ms/u/s!Aq9gkv5xCmlOg6lu0yTHDwJTx1ZYtA?e=LwmHBQ
Kevin
any timer on alieexpress or so wil do it
But then instead of a timer we use a little Arduino, who measures the pump current….switches on …if no water wait a set period, then pumps again. If twice there is no water, the wait interval is double and keeps doubling until it is 3 days…if it encounters water, it pumps until dry and waits, if the 2nd time it encounters again water it will half the wait time etc…
Have not added an alert if the interval is less than 5 minutes…
@jan-kees Could you share the code and instructions you used for your Arduino? And hopefully at a level that a person with minimum programming skills could duplicate?
I’m hoping to connect the discharge for my bilge drying system into the drain hose for my sink.
I’d be curious to know what methods people have used to tap into hoses to drain the water from the bilge drying system.
I tapped into the hoses for my hatch drains that are shared by the cockpit scuppers. Just pressure fitted the 3/8″ hose into a hole drilled in the top of the drain hoses. No issues at all.
Kevin
Mine went into my shower sum as it was lower.